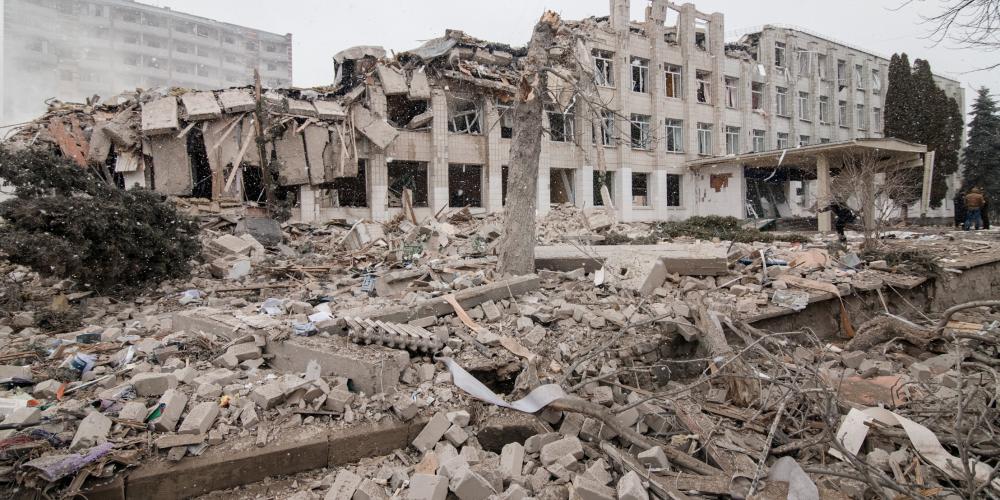
Hubert Rahier, professor of physical chemistry at the VUB Materials & Chemistry research group, has been asked by the Ukrainian company Sheldor to help recycle concrete from buildings destroyed by the Russians. Rahier, with Dutch and Belgian partners and with funding from a European Interreg project, has developed a method of fully recycling concrete, including a large part of the cement, after which the raw materials can be used again to make high-quality structural concrete.
âConcrete consists of aggregates such as stones or gravel, sand and a binder, usually cement,â explains Rahier. âYou can extract all those components from the concrete: sand and gravel come loose from the concrete if you grind it mechanically in a particular way. The finer part containing the hydrated and thus âfinishedâ cement must then be reprocessed until it becomes usable again as a binder.â
For the various steps involved in extracting the constituent parts from the concrete, Rahier works with various partners from Belgium and the Netherlands, each of whom applies their expertise in their own fields. A Dutch company has developed a smart crusher that will mechanically reduce the concrete in a specific way. âThat machine not only breaks up the concrete, it also rubs off the finer particles and spares the gravel in the process. The crusher simultaneously separates the sand from the finer cement,â says Rahier. âOur initial experiments showed that the gravel was also pulverised, making the cement part unusable for recycling.â
To recycle the binder too, the various fine parts must first be separated until only the cement remains. âTo make that hydrated cement usable again and soak it out of its chemical bond until you have a reactive powder, the cement powder is heated to between 500 and 600°C in a specially designed high-powered microwave oven. This uses electricity generated by solar panels, at our partner Rutte in Zaandam, so the whole process can be done without additional carbon emissions.â A PhD student from Leuven is working on fine-tuning that process, with the Belgian machining manufacturer MEAM.
Rahierâs process recently came to the attention of a Ukrainian business leader who wants to use it to recycle the concrete of bombed-out neighbourhoods in Ukraine. He wants to use it to rebuild, on the ground, the cities that are now in ruins. âNegotiations are going smoothly but there are still some improvements to be made to the smart crusher,â says Rahier. âWe should be operational by the end of the year. Today, all the ingredients of old concrete can be recycled and you can make concrete of the same quality, possibly with the addition of some extra binder or cement. So we make new concrete with almost 100% recycled elements. The CO2 gain you can make with our process is huge and, whatâs more, you donât need any additional raw materials from nature.â