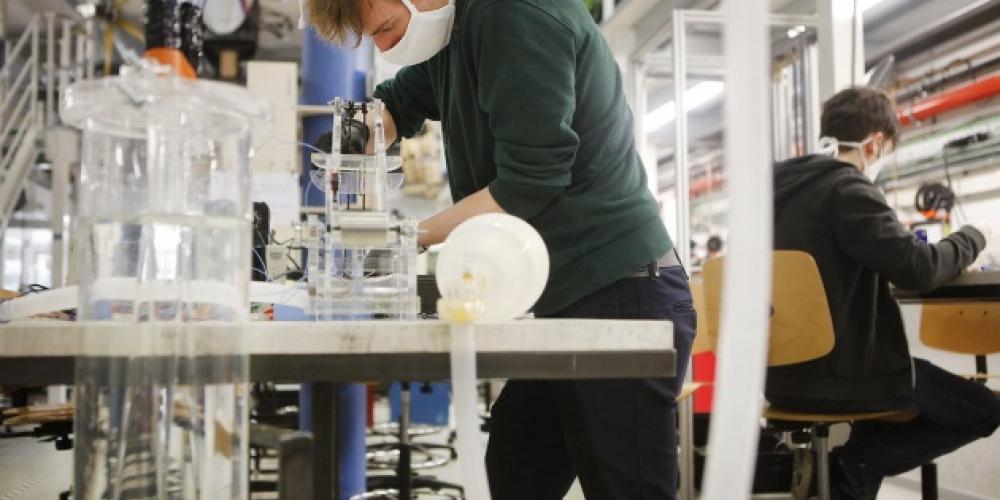
Tim Hertsens didnât have to think twice when the email popped up in his inbox. Might he, VUB alumnus, be able to help his old FabLab Brussels team with their project to develop a ventilator prototype?
Grabbing a sleeping bag and a sweater, he left Den Helder in the Netherlands, where he lives and works, to return to the place where he first learned to wield laser cutters and 3D printers during his electromechanics studies.
Sleeping in researchersâ offices
So, every night for the next weeks, Hertsens would roll out his sleeping bag and bed down in the FabLab researchersâ offices. âItâs a four-hour ride to Den Helder. There wasnât really another solution, and I didnât mind it. Iâve done it before, both with Defence and with the scouts when I was younger. It wasnât a big hurdle for me,â he says, laughing.
Hertsens, 29, is a technical officer with the Marines, supervising the maintenance of Belgian and Dutch vessels. He requested permission to help the FabLab workshop in Brussels play their part in tackling the coronavirus; the lockdown measures had already reduced his normal workload. And isnât this what Defence is all about: helping civilians?
âI felt like I would be of more use to the common good at the FabLab than working on a ship in Den Helder. Of course, this had nothing to do with my Defence job, but I was glad that I could do something meaningful with the other alumni, with FabLab, during this corona crisis,â he explains. âThe FabLab is also a place where you can make so many things; it would be a waste not to use a lab with this many facilities during a period like this.â
âIt would be a waste not to use a lab with this many facilities during a period like this.â â Tim Hertsens, VUB alumnus
Finetuning till 3am
Ever since the coronavirus crisis arrived in Europe, experts have warned about a potential ventilator shortage that could have deadly consequences, given the expected influx of critically ill patients. Itâs why a team of 40 engineers, IT specialists, programmers and designers decided to band together three weeks ago to develop a handful of ventilator prototypes, each model an improved version of the last.
Their goal: to come up with a properly functioning prototype as quickly as possible. âEspecially in the beginning, youâre working with prototypes and you donât know whether they will work 100%. So we finetuned them day and night, often until 2, 3 oâclock in the morning,â Hertsens explains. âBecause youâre working toward results, you keep working until youâve achieved that result. It was really exhausting, but you pushed back that exhaustion because of the results you achieved, which also motivated you to keep working.â
If all goes according to plan, a functioning prototype will be ready in a week â thanks to the efforts of the FabLab team, but also of the companies, partner organisations and research centres that offered support, feedback and materials, like Audi Brussels, UZ Brussel and Flanders Make.
Surreal student experience
It feels almost surreal at times, says Jonathan Sterckx, 23, project leader and masterâs student in industrial sciences. Both the speed at which the project took off and with which the team kept growing, and the responsibility handed to the students. âWeâd agreed to try to build a prototype over a period of three days. And a week later, we were suddenly talking to Flanders Make and Audi Brussels, and fielding emails from CEOs of some of Belgiumâs largest companies, all wanting to help.
âItâs a unique opportunity to experience such a project from a front-row seat as part of our study programme. Weâve been trained to develop rapid prototypes over a period of 12 to 18 months â not to build a medical prototype in two weeks. Thereâs also so much more to the project than just the development part. The core group of students who got the project started are no longer designing. Theyâre no longer holding screwdrivers; theyâre now guiding people on the outside working at private companies.â
âItâs a unique opportunity to experience such a project from a front-row seat as part of our study programme.â â Jonathan Sterkcx, master student indusrial science
Itâs a student-led project; thatâs maybe what makes it unique. âWhen we do a Skype call with a company for the first time, theyâre always a little shocked when we told them we were students,â Sterckx explains. âBut they always really want to continue working with us. And their confidence gives us a positive vibe.â
If all goes well, a working prototype will soon be finished - thanks to the hard work and efforts of the team, but also of the companies, partner institutions and research centres that offer support, feedback and material - from Audi Brussels and UZ Brussel to Flanders Make.
Read further below the image
The design of prototypes for ventilation equipment is a project conducted by VUB students.
A one in 10 chance
When they started, fluid mechanics professor and FabLab academic supervisor Mark Runacres figured they had a 10% chance of succeeding in their aim â to develop a ventilator prototype that could quickly be produced on a large scale. âI know that we do things well, but I didnât expect us to come up with a working prototype so quickly,â he says.
Still, FabLab Brussels was the perfect team to get the job done. The open-source workshop for students, researchers and hobbyists has always had a can-do attitude, exemplified by its "Prototypes not PowerPoints" motto. âOf course, you have to perform simulations every now and then, but itâs also possible to continue asking yourself whether something might work for too long,â Runacres adds. âOur attitude has always been: âCome on guys, donât whine. Build it and then we can test whether it works.ââ
âCome on guys, donât whine. Build it and then we can test whether it works.â â Prof. Marc Runacres, FabLab Brussels
FabLab Brussels got permission to remain open mid-March and is currently a hive of activity in the otherwise abandoned Usquare site in Elsene. If you were to enter the workshop this week, youâd see students over two floors, huddled behind tables and laptops, everyone wearing face masks and gloves, everyone hard at work. At the centre of the ground floor is the device that the past few weeks have revolved around â the most recent prototype.
Madness and fuzzy feelings
It may seem chaotic, but there is a method to the madness. âWe transformed into a company over the last two weeks. Before we were academics, and slightly anarchist at that. Today we have a tight structure with teams and team leaders, and we respond to things much more quickly even though thereâs 40 of us and weâre working against tight deadlines,â Runacres explains.
In spite of the time and performance pressure and the new organisational structure, there have been barely any conflicts. Instead, there is a great deal of unity, he adds. âEveryone here was doing the thing he or she excelled at and knew exactly why they were doing it. And that created a lot of positive energy. Iâm almost afraid to say it, but a lot of people also really had fun here,â he says.
âIâm unbelievably happy with what we achieved and so proud of the team. When I see how good these boys and girls are, I feel super proud and get a warm, fuzzy feeling.â
Donate oxygen
To test the prototypes, additional resources are needed: âŹ5,000 per device. The faster the ventilation machines are tested, the faster they can go into production to save lives in the intensive care units. In Belgium or elsewhere.
If you want to support this wonderful initiative, you can do so at www.vub.be/fablabvoorzuurstof.